Recommendations for Specific Grease Fittings
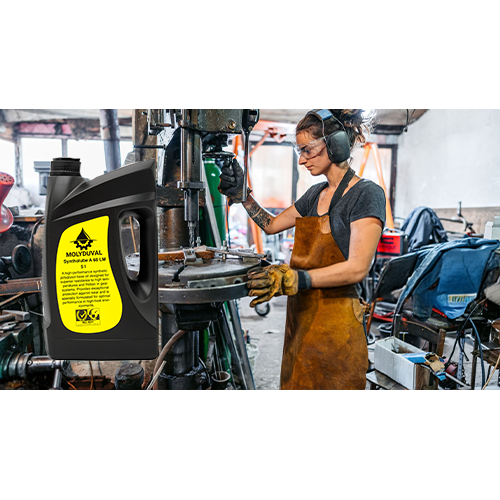
SOLANO Recommendations for Grease Fittings and Tips for Their Installation and Maintenance
Recommendations for Specific Grease Fittings
Standard Applications (General Machinery & Vehicles)
- Type: Straight or angled grease fittings.
- Material: Zinc-plated steel or stainless steel (for corrosion resistance).
- Example:
- SAE Standard: 1/4"-28 UNF thread straight grease fittings.
- Metric Standard: M6 x 1.0 straight grease fittings.
Tight Spaces or Obstructed Areas
- Type: 90-degree or 45-degree grease fittings.
- Material: Stainless steel for durability.
- Example: M8 x 1.0 90-degree grease fittings for confined lubrication points.
Heavy-Duty Applications (Construction & Industrial Machinery)
- Type: Button-head grease fittings.
- Material: Case-hardened steel for high-pressure tolerance.
- Example: 5/8"-18 UNF button-head fittings for mining or construction equipment.
High-Temperature or Harsh Environments
- Type: Stainless steel grease fittings or pressure-relief fittings.
- Material: Stainless steel or brass for resistance to heat and corrosion.
- Example: M10 x 1.0 pressure-relief fittings.
Older or Specialized Equipment
- Type: Flush or pin-type fittings.
- Example: 1/8" NPT flush grease fittings for older industrial tools.
Installation Guidelines
Prepare the Installation Area
- Clean the hole or port where the grease fitting will be installed to remove dirt, grease, or debris.
- Check for thread compatibility (SAE, metric, or pipe threads) to ensure a proper fit.
Apply Thread Sealant (Optional)
- For threaded fittings, use a thread sealant or tape for a leak-proof connection.
Install the Fitting
- For threaded fittings: Screw them in using a wrench or socket until snug. Avoid overtightening to prevent damage.
- For drive-type fittings: Use a mallet or hammer to gently tap them into the hole.
Test the Connection
- Attach the grease gun coupler and apply grease to verify that it flows smoothly into the lubrication point.
- Check for leaks or grease ejection from unintended areas.
Maintenance Tips
Regular Inspection
- Periodically check fittings for clogs, damage, or corrosion.
- Replace damaged or corroded fittings immediately to maintain lubrication effectiveness.
Unclogging Fittings
- Use a fitting unblocker tool to clear clogs caused by dried grease or debris.
- Soak stubbornly clogged fittings in a solvent like kerosene before cleaning.
Grease Compatibility
- Ensure that the grease used is compatible with the fitting and the equipment's specifications (e.g., NLGI grade and type).
Protect Fittings
- Install caps or covers on grease fittings to prevent dirt and contaminants from entering.
Avoid Over-Greasing
- Apply grease gradually and stop once resistance is felt to prevent over-pressurizing seals or bearings.
Recommended Tools and Accessories
- Grease Gun Couplers: Lock-on grease couplers for secure attachment.
- Grease Fitting Assortment Kit: Includes various types and sizes of grease fittings for multiple applications.
- Grease Fitting Installation Tool: For inserting or removing fittings easily.
- Grease Fitting Caps: Prevent contamination when fittings are not in use.
- Unblocker Tool: Clears clogged grease fittings quickly.